Electroplating is essential for many automotive, aerospace, construction and other critical manufacturing applications. Electroplating is essential for several reasons, including improving part and equipment longevity, enhancing electrical conductivity, minimizing corrosion and making parts more aesthetically pleasing. Many alloys and metals play a role in the process, but zinc and nickel plating have the most widespread applications within the automotive and aerospace industries.
Zinc-nickel plating also has multiple applications, as it provides corrosion resistance in the harshest environments and meets electronics, automotive and aerospace industry standards. A comparison between nickel and zinc plating is necessary to ascertain which is better for your specific application. Both types of plating have advantages and disadvantages, and exploring them will provide you with the essential information to make the right choice for your business.
Nickel Plating
Nickel plating is a form of electroplating that requires applying nickel to the surface of a substrate in a thin layer. Once the substrate surface is clean of dirt and debris, it gets immersed in an electrolyte solution. The process requires particular processes to deliver quality plating, including temperature regulation and pure, distilled water in the electrolyte solution. In general, nickel plating is an excellent way to enhance various metals’ durability, appearance and functionality, including aluminum, brass and steel.
Nickel Plating Pros and Cons
Nickel plating has many advantages, including the following.
- Cost-effectiveness: Preventing metals from corroding can be expensive, but nickel plating can be one of the most cost-effective ways of providing this protection.
- Increased product life span: Nickel’s durability and corrosion-resistant properties help improve products’ overall longevity.
- Improved appearance: Nickel provides an attractive finish to parts, which is ideal for applications requiring functionality and aesthetic appeal.
- Enhanced electrical conductivity: Nickel is an outstanding electrical conductor. It’s a perfect choice for electrical components and appliances, providing conductivity with limited corrosion and degradation over time.
- Resistant to high temperatures: Nickel can resist high temperatures, which is excellent for applications with high friction and many moving parts, such as automotive and aerospace.
- Limited maintenance: Nickel-coated parts have an extra layer of durability. After installation, components require little maintenance. Often, a mild commercial detergent will be ample to keep them functional and attractive.
Like any finishing process, nickel plating has its challenges, which include the following.
- Energy requirements: The nickel plating process requires a high energy output.
- Environmental considerations: Waste management processes must be extensive, which can be costly.
- Limited lubrication: Nickel plating can limit a part’s ability to lubricate itself, which causes friction in areas where there is constant motion.
- Removal challenges: After installation,nickel plating can be challenging to remove.
- Allergy risks: People who come into direct contact with nickel may suffer skin irritations and allergic reactions.
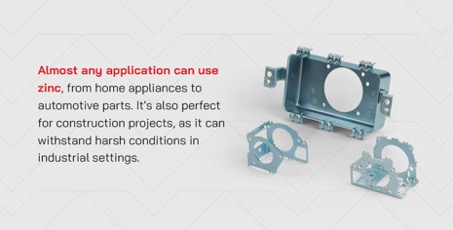
Zinc Plating
The automotive industry widely uses zinc plating, which has been a staple for almost 100 years and is a well-proven plating system. In addition to electroplating, zinc plating involves electro-galvanization, or applying a thin layer of zinc directly to the surface. While the process has many benefits, it’s best to understand where zinc plating has its most successful applications.
Zinc Plating Pros and Cons
Zinc is a remarkably stable and reliable metal in many applications. Some of the benefits of zinc plating include the following.
- Enhanced corrosion protection: Rust can lead to weakened parts and reduced mechanical performance. Zinc plating adds an extra layer of protection against rust and provides reliable precision parts for automobiles, airplanes and many other applications.
- Improved mechanical strength: Manufacturers often use zinc because it can withstand harsh environments.
- Cost-effective application: Zinc is abundant and easy to work with, so it provides manufacturers with a cost-effective option.
- Unparalleled versatility: Almost any application can use zinc, from home appliances to automotive parts. It’s also perfect for construction projects, as it can withstand harsh conditions in industrial settings.
- Improved customer satisfaction: Manufacturers can wow their customers with zinc plating. Not only does the process provide rust protection and a long-lasting finish, but it also has that extra aesthetic touch.
- Improved ductility: Alkaline Zinc Plating is able to be formed, crimped, or bent.
While zinc plating is an excellent addition to many manufacturing applications, consider the disadvantages carefully to ensure adequate preparation and the best possible results. The downsides of zinc plating include the following.
- Galvanic corrosion: Combining zinc with dissimilar elements in a water-based setting can cause galvanic corrosion — a reaction between the two metals, resulting in both corroding.
- Friction resistance: Zinc plating isn’t ideal for applications where metal parts contact each other and create friction.
- Production costs: While zinc is more cost-effective than many other metals, large-scale applications can be expensive. Production costs can be prohibitive.
- Environmental limitations: Bulky corrosion can occur when zinc plating is in marine or tropical environments or confined areas with heavy condensation.
Nickel vs. Zinc: A Comparison
While both plating options have pros and cons, each is suitable for different applications. Choose which is more suitable for your needs based on a thorough comparison of the two. Some key points to consider when comparing zinc and nickel include the following.
- Processes: Zinc and Nickel plating occurs through electroplating, or electrogalvaniz.
- Energy use: The zinc plating process requires less energy than nickel plating. The energy costs of nickel plating are higher.
- Cost: Production costs are the opposite of energy costs. Nickel plating costs are less expensive compared to zinc plating production, as the process requires less sophisticated equipment.
- Recycling capabilities: Zinc is recyclable, making it a more sustainable and cost-effective option for some applications.
- Plating flexibility: Nickel plating offers manufacturers more flexibility in terms of thickness and volume.
- Aesthetic advantages: Nickel plating offers a brighter finish in most cases, though plating manufacturers can provide many zinc plating options to enhance customer satisfaction.
- Coating life span: Zinc plating provides a more long-term option. The coating in nickel plating has limited longevity.
Zinc-Nickel Plating
As technology has improved, a zinc-nickel alloy has become more accessible to manufacturers. Like any plating technique, zinc-nickel isn’t universally applicable, but the alloy provides manufacturers with many advantages. The principal advantage is enhanced corrosion resistance, as zinc-nickel coating lasts longer in a corrosive environment. Other benefits of zinc-nickel plating include the following.
- Less passivization and top coat requirements: The plating doesn’t require as much maintenance due to the enhanced corrosion resistance.
- Reduced galvanic potential: A zinc-nickel alloy is more suitable for applications where different metals come into contact, as there is less chance of galvanic corrosion.
In some cases, zinc or nickel may be the more straightforward option. Their applications are well-understood and their processes are less complex. Understanding which plating technique is best for your application depends on your project’s size and scope and the parts’ intended use. Consider consulting a specialist for more detailed information.
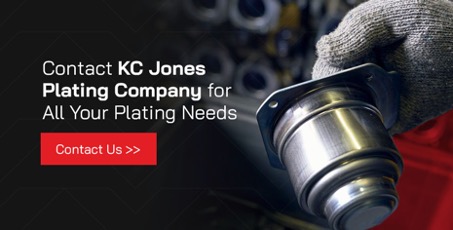
Contact KC Jones Plating Company for All Your Plating Needs
For automotive plating and finishing, perfection is the only option at KC Jones Plating Company. We are an industry-leading plating company with decades of experience. When you partner with us, you can rest assured your parts will be corrosion-resistant, durable and robust.
No matter your requirements, we will do our best to find an ideal solution for you. We have a reputation for helping our customers tackle their toughest challenges, from coating complex parts to developing new coating solutions. Please feel free to contact us and learn more about how our quality plating creates safe parts for you.